Energy monitoring has evolved from a mere necessity to a strategic advantage for forward-thinking companies. Understanding the nuances of energy consumption and its impact on operational efficiency is crucial for manufacturing industries. By delving into granular details, such as energy consumption patterns, power quality, and power factor, businesses can optimize their processes, reduce costs, and minimize their environmental footprint. It's not just about having the numbers; it's about leveraging data-driven insights to optimize resource allocation and enhance productivity. The ability to measure and manage energy usage is the first step towards transforming your business into an agile and future-ready enterprise.
In our previous blog post, "The Benefits of Monitoring Energy Consumption, Quality, and Power Factor," we explored the significance of monitoring energy variables and the advantages it brings to industrial operations. We will now dive deeper into the practical applications of this information and how it empowers businesses to drive sustainability, optimize energy consumption, and reduce costs.
Ensuring ESG Goals and Measuring Environmental Impact
By leveraging data obtained from Programmable Logic Controllers (PLCs) or non-intrusive sensors, businesses can gain real-time visibility into energy consumption at various levels, including power supplies, substations, and individual machines. This comprehensive monitoring capability enables the identification of energy efficiency opportunities and the implementation of targeted measures to reduce energy waste, ultimately contributing to a lower carbon footprint.
Furthermore, energy monitoring provides insights into the energy consumption associated with each unit or SKU produced. By accurately calculating specific energy usage per product, organizations can evaluate the energy efficiency of different product lines, identify areas for improvement, and align their energy consumption with sustainable practices. This data-driven approach empowers businesses to make informed decisions that optimize resource allocation, enhance productivity, and reduce their overall environmental footprint.
For example, we accurately track energy consumption per batch to calculate key performance indicators (KPIs) for the food and beverages industry. By contextualizing production variables with available data, we help our clients gain valuable insights into resource consumption and identify areas for improvement. The solution facilitates the calculation of energy usage per unit of a specific SKU, aiding in optimizing resource allocation and production processes.
The ability to gain visibility into the energy consumption of individual SKUs empowers businesses to develop targeted strategies for energy optimization. By identifying energy-intensive processes or products, organizations can implement measures to reduce energy waste, improve efficiency, and ultimately lower their overall energy footprint.
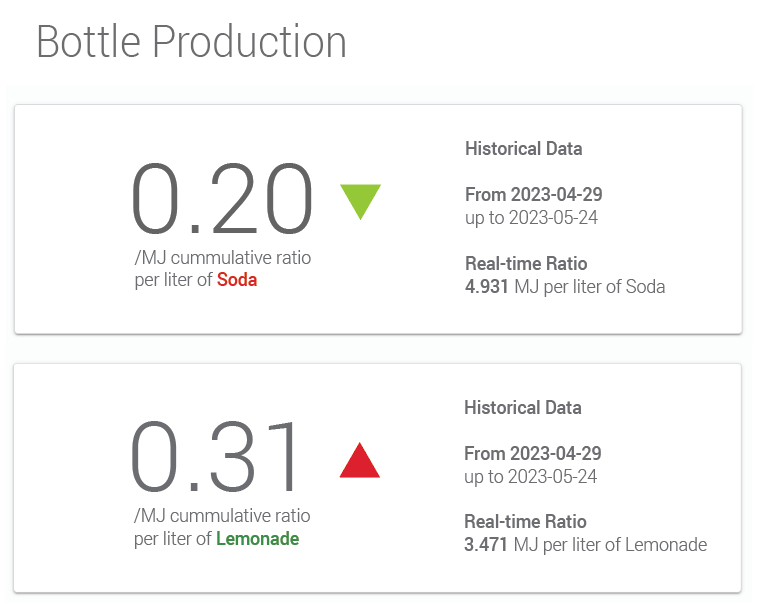
Image of our energy monitoring application showing daily energy consumption (MJ) per liter of a beverage, indicating whether each SKU has a higher or lower than average consumption.
Smart Energy Consumption through Data-Driven Insights
Just like any other IIoT application out there, energy monitoring generates thousands of data points each day. The question is, how can it be harnessed to take this solution to the next level? The answer lies in data science and advanced analytics that generate actionable insights. By analyzing the wealth of data collected from energy monitoring systems, we help businesses develop sophisticated algorithms tailored to their specific requirements. These algorithms provide recommendations that optimize energy consumption and costs, ensuring high-tech industries operate at peak efficiency. Some examples include:
- Optimized Production Scheduling: By leveraging historical energy data and considering external factors such as electricity price fluctuations, organizations can develop algorithms that recommend optimal production schedules. This approach allows businesses to adjust production activities to minimize energy costs during peak hours, resulting in significant cost savings.
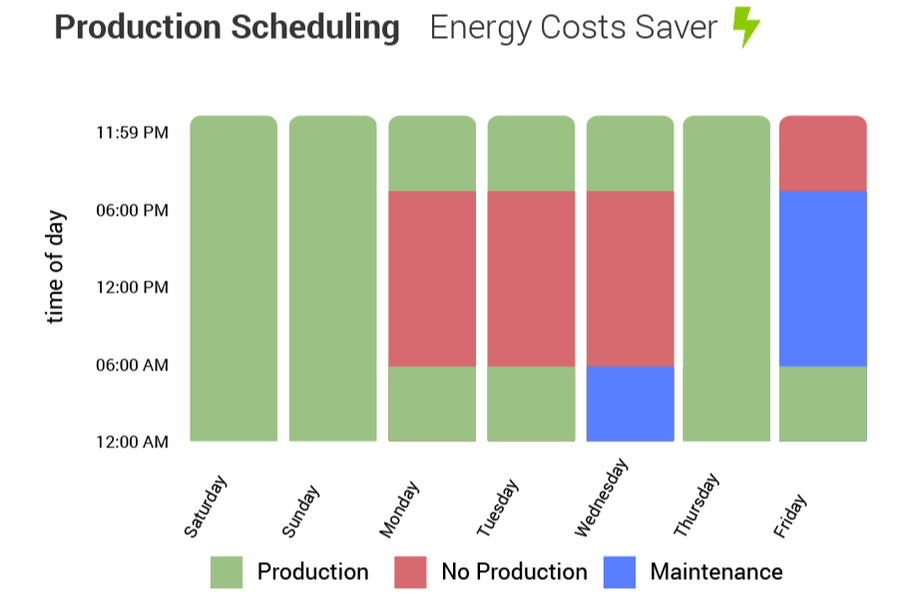
- Load Balancing and Machine Rotation: Data-driven insights enable businesses to identify opportunities for load balancing and machine rotation. By redistributing energy-intensive tasks across machines or prioritizing the use of energy-efficient equipment, organizations can optimize energy consumption, prolong machines’ lifespan, and enhance operational efficiency.
- Identifying Energy Inefficiencies: Energy monitoring data can help detect machines or processes that consume excessive energy when inactive or operate inefficiently. By identifying these inefficiencies, businesses can take corrective actions to reduce energy waste and improve overall energy efficiency.
If you want to read more about the transformative power of energy monitoring for your business, explore our energy monitoring use case. Learn how a CPG company achieved remarkable results, saving 15% on their energy bill for a 200 MW operation while significantly reducing their carbon footprint through the monitoring of energy consumption, quality, and power factor.
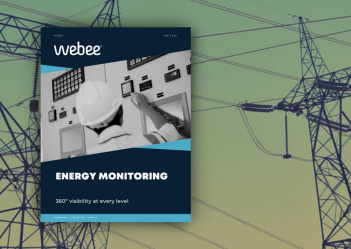
The benefits of industrial energy monitoring are now clear. By capturing and analyzing energy-related data, organizations can gain deep insights into their operations, identify areas of improvement, and make data-driven decisions that drive performance.
Webee's energy monitoring solution provides the necessary tools and capabilities to transform energy data into actionable insights, enabling businesses to achieve their ESG goals, reduce their environmental impact, and positively impact their bottom line. By leveraging advanced analytics and data science, organizations can unlock the true potential of energy monitoring and drive their journey toward a more sustainable and future-ready enterprise. If you are ready to take the next step don't hesitate to schedule a demo now.